
S.E.P are the only NZ company who have built their own machine to manufacturer Stainless steel wire mesh cable trays.
Our wire mesh cable trays are fabricated using: 5mm—T304 / ½ Hard Tempered Stainless Steel Rod. This rod is sourced from overseas and has been manufactured to the International specification Din 1.4571 (V4A) AISI 316 TI. Characteristics of the material used and the finished product have been designed to meet the most demanding requirements of electrical industry.
Individual units have a standard length of 3metres; side walls of 60mm, with width variations of 60mm,100mm,150mm,200mm,300mm,400mm,450mm,500mm & 600mm.
In the smaller sizes, 60mm,100mm and 150mm we also manufacture with 30mm side walls.
Our Stainless Steel Wire Basket Cable Trays allow air circulation to keep wiring cool and offer good resistance to corrosion in natural and food atmospheres.
S.E.P also offer pre-made horizontal bends, internal risers, external risers and horizontal ‘T’ sections. We also manufacturer and supply universal joining plates, joining clamps, joining strips, hanging brackets, side supports, centre divider, conduit supports & mounting brackets.
All accessories are supplied pre-drilled complete with M6 x 16mm Coach bolt and Flange Nuts as required. Units can be welded together on site; a Quick Fit range of accessories is also available.
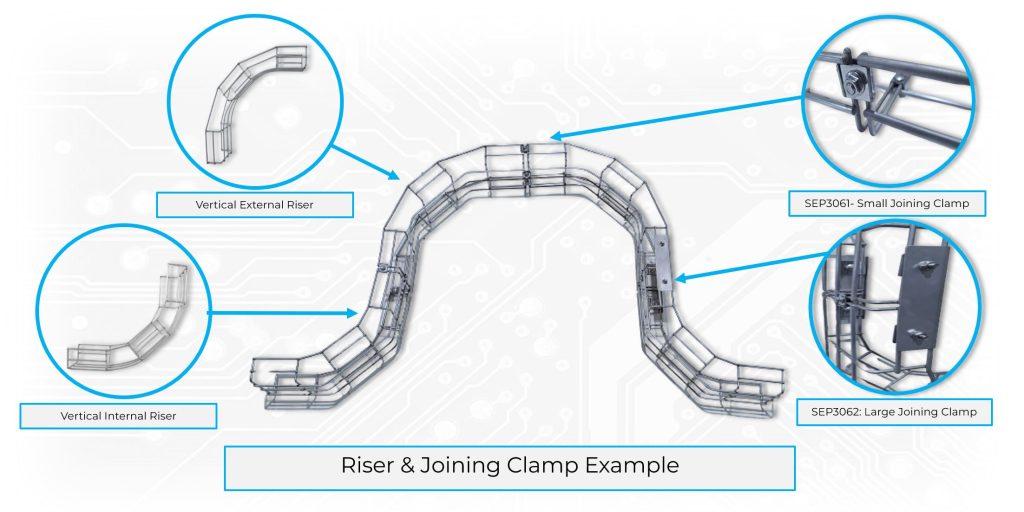
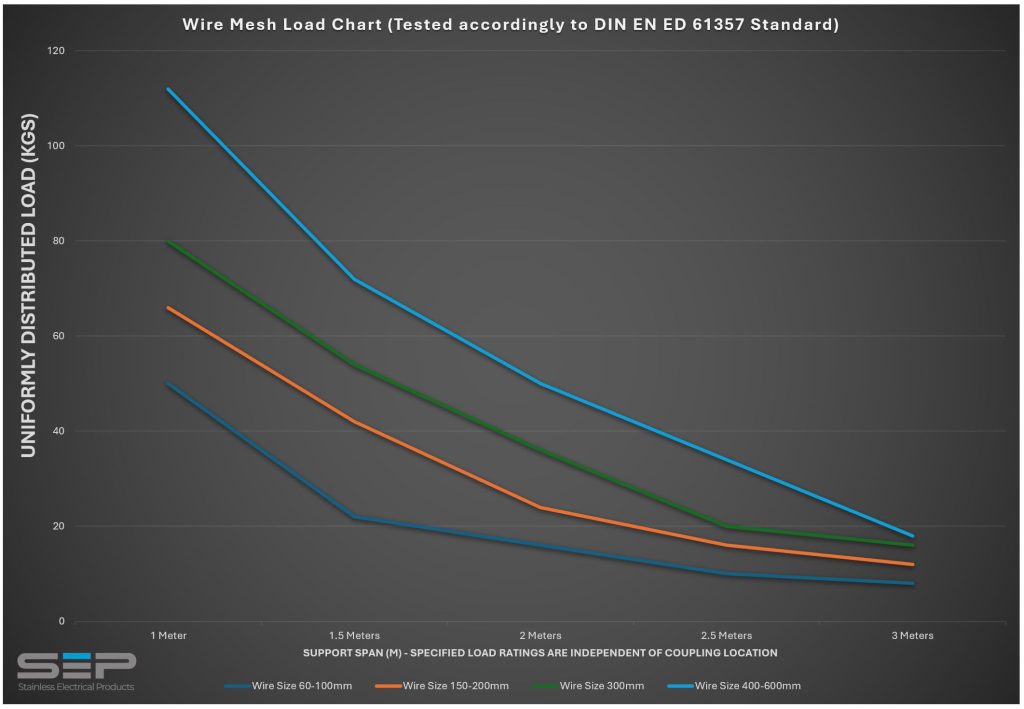
Using wire mesh cable tray systems involves selecting the right components, planning the layout, and following precise installation steps. Proper installation ensures efficient cable management, safety, and compliance with standards.
Click the image below to download Technical Information
Please contact us to discuss your requirements